BoDo II - The SAHM BobbinDoffer
In its latest generation, the mobile, fully automatic doffing and transport system BoDo II is once again setting new standards in bobbin and tube handling. The pick-up of bobbins at the winding machine as well as the set-up with empty tubes is performed entirely automatically – just like the transport of bobbins and their delivery to freely defined locations in the production workflow.
Working with centralized fleet management software, BoDo II robots operate as genuine team players and enable continuous 24/7 operation with an outstanding level of efficiency.
Bobbin handling. 24/7. Fully automatic.
Bodo II is the innovative solution for fully automatic bobbin and tube handling. It can be flexibly integrated into existing processes and enables round-the-clock operation. Physical strain on operators is reduced, processes are optimized – all with increased speed, efficiency, cost-effectiveness and ergonomic optimization.
![[Translate to 03 - Chinesisch:] SAHM BoDo II. Complete machine concept. [Translate to 03 - Chinesisch:] Overview of a complete machine concept consisting of tube depot, SAHM winding machine and SAHM BoDo II.](/fileadmin/_processed_/3/3/csm_CONTENT_BoDoII_01_186863c9b5.jpg)
![[Translate to 03 - Chinesisch:] Tube pick-up. [Translate to 03 - Chinesisch:] Detail photo of SAHM tube depot. Pick up of an empty tube by the BoDo II handling robot.](/fileadmin/_processed_/6/9/csm_TEASER_BoDoII_01_f770703c0b.jpg)
TUBE PICK-UP
![[Translate to 03 - Chinesisch:] Bobbin doffing [Translate to 03 - Chinesisch:] Doffing of a full bobbin and take up of the full bobbin by the BoDo II handling robot.](/fileadmin/_processed_/3/5/csm_TEASER_BoDoII_02_2a6097c7d7.jpg)
BOBBIN DOFFING
![[Translate to 03 - Chinesisch:] Tube placement. [Translate to 03 - Chinesisch:] Placement of the empty tubes on the SAHM winding machine by the BoDo II handling robot](/fileadmin/_processed_/7/4/csm_TEASER_BoDoII_03_1162cdf8f2.jpg)
TUBE PLACEMENT
![[Translate to 03 - Chinesisch:] Bobbin delivery. [Translate to 03 - Chinesisch:] Delivery of the full bobbin to a creel trolley by the BoDo II handling robot.](/fileadmin/_processed_/a/d/csm_TEASER_BoDoII_04_76f57c00fd.jpg)
BOBBIN DELIVERY
![[Translate to 03 - Chinesisch:] Charging station. [Translate to 03 - Chinesisch:] BoDo II charging station](/fileadmin/_processed_/2/9/csm_TEASER_BoDoII_05_f1a5e22b13.jpg)
CHARGING
Freely definable radius of movement
Whether defining driving routes or pick-up and delivery points for bobbins and tubes - BoDo II is freely programmable and can be adapted to any production environment. With identical plant design, BoDo II units can even be exchanged between plants for cross-plant use.
Exact positioning
![[Translate to 03 - Chinesisch:] BoDo II's sensors and cameras](/fileadmin/_processed_/9/a/csm_CONTENT_BoDoII_02_6bc885ab87.jpg)
Exact positioning
With its integrated sensors and cameras, BoDo II perceives its surroundings and independently selects the most efficient route. Obstructions in the floor surface or areas that cannot be properly navigated can be easily defined in the software and will be by-passed by BoDo II.
Intelligent fleet management
![[Translate to 03 - Chinesisch:] BoDo II robots are linked via intelligent fleet management software.](/fileadmin/_processed_/3/0/csm_CONTENT_BoDoII_03_f8d2067814.jpg)
Intelligent fleet management
BoDo II robots communicate with SAHM winding machines and are linked via intelligent fleet management software. This net-working enables fully optimized logistic and process workflows for the realization of a Smart Factory environment.
360° environment detection
![[Translate to 03 - Chinesisch:] BoDo II checks the environment](/fileadmin/_processed_/b/5/csm_CONTENT_BoDoII_04_5584176595.jpg)
360° environment detection
As a collaborative system, BoDo II ensures safe operation in conjunction with people, vehicles and machines. Two integrated safety laser scanners continuously monitor the surroundings and provide BoDo II with all safety-relevant information. When an obstacle is detected, BoDo II reacts on the basis of the actual real-time situation. Not being bound to a track, BoDo II can sim-ply drive around the obstacle, search for an alternative route or stop immediately, if required in an emergency situation. And all of this is done fully autonomously - without operator involvement.
Solutions for any production capacity
Solutions for any production capacity
BoDo II is a flexible, scalable system which offers a suitable solution for every production operation and for any output. Whether operating singly or with multiple networked BoDo II units – the system can be individually adjusted to all customer requirements and process details. And can be modified as required – making BoDo II the perfect future-proof choice.
![[Translate to 03 - Chinesisch:] BoDo II, 1 tier, 2 tiers and 3 tiers](/fileadmin/_processed_/0/0/csm_PAGETEASER_BoDoII_210c9dfe07.jpg)
APPLICATIONS
Continuous processes in combínation with automatic SAHM winding machines, e.g.: TWINSTAR II (others on request)
FEATURES
- Simultaneous removal/placement of multiple bobbins (with 2 and 3-tier models)
- Two safety laser scanners for 360° environment detection
- Autonomous, trackless driving
- Intelligent fleet management system
- Teaching of bobbin doffer via mobile device
OPTIONS
- Creel trolley
- Tube depot
- Possibility of integration into DCS (Distributed Control System)
Technical data
BoDo II 1 tier | BoDo II 2 tiers | BoDo II 3 tiers | |
Load capacity | 25 kg | 50 kg | 75 kg |
Speed | 1 m/s (loaded) | 1 m/s (loaded) | 1 m/s (loaded) |
Battery runtime | 7 h (charging time 2 h) | 7 h (charging time 2 h) | 10 h (charging time 1 h) |
Safety Features | Safety laser scanners, 3 D cameras | Safety laser scanners, 3 D cameras | Safety laser scanners, 3 D cameras |
Tiers | 1 | 2 | 3 |
Navigation | Automatic selection of most efficient route without track | Automatic selection of most efficient route without track | Automatic selectrion of most efficient route without track |
Tube inside diameter | 94 mm*) | 94 mm *) | 94 mm *) |
Tube outside diameter | 100 - 108 mm *) | 100 - 108 mm *) | 100 - 108 mm *) |
Tube length | 290 mm *) | 290 mm *) | 290 mm *) |
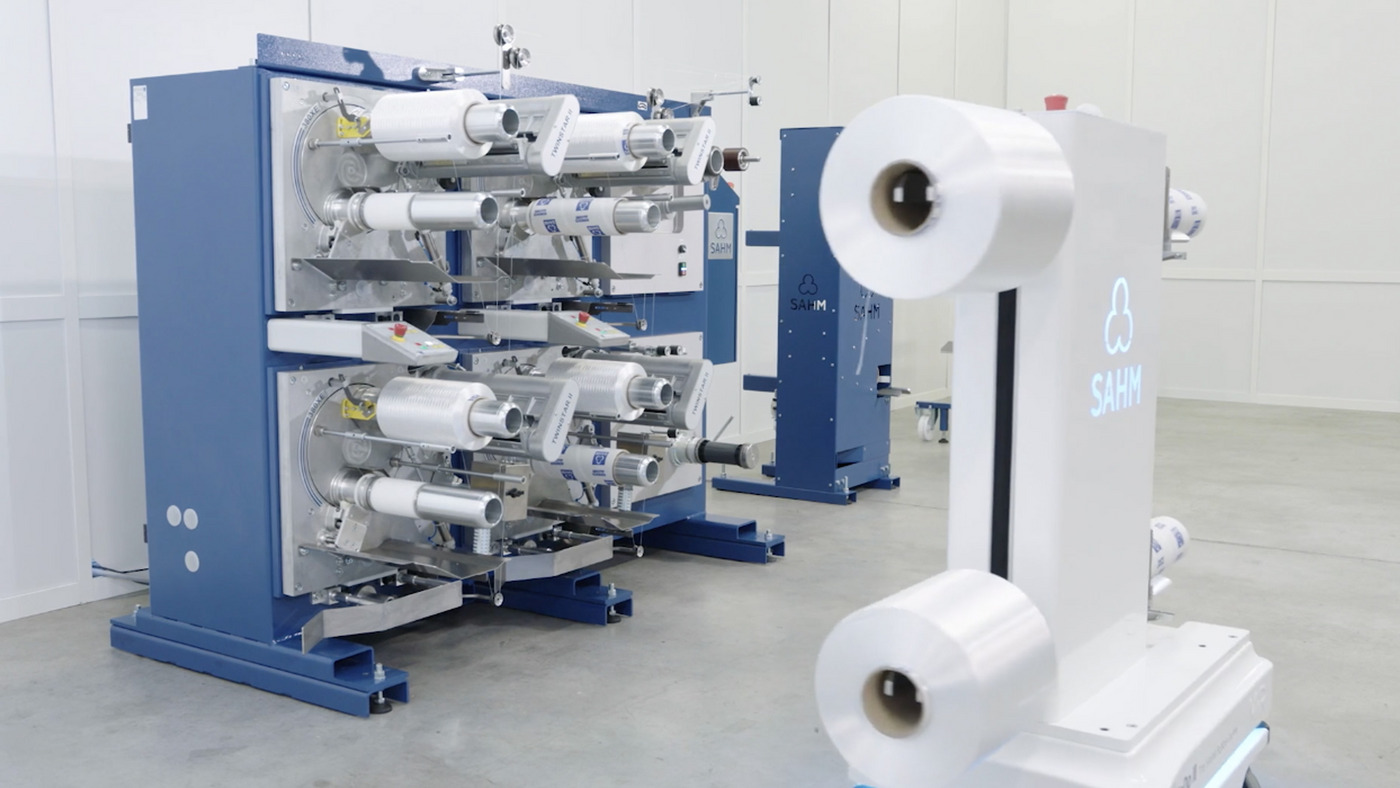